Conveyor Rollers & Pulley
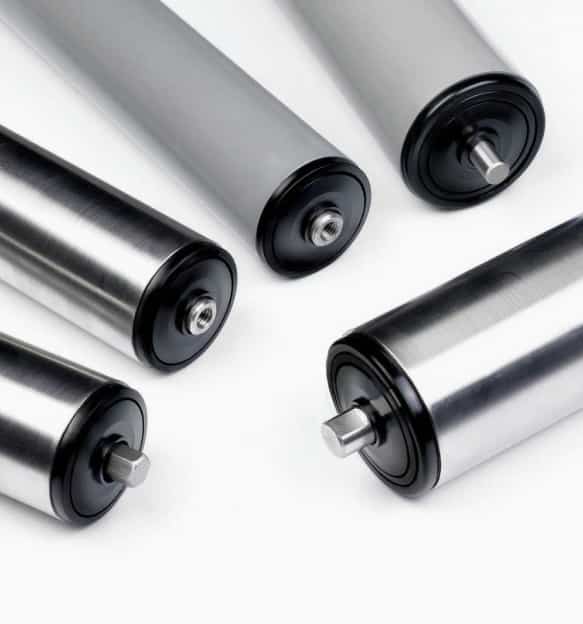
Our partners give careful consideration to each and every manufacturing stage, from initial research to design, from production to exact laboratory tests using specifically created machinery to examine conveyor rollers’ performance. The idler produced by our partners have a low radial runout rate, which greatly improves the stability of material conveying, and has low rotational resistance, which will improve the service life of the conveyor belt. Aiming at various harsh use environments such as mines, coal mines, and chemical industries, the high-sealing, high-life and low-resistance rollers developed by our company have achieved good application results, with a service life of more than 40,000 hours.
Additionally, because roller bearings are protected by an effective sealing system and are made of highly selected materials like steel and thermoplastic, they are able to withstand environmental stresses like dust, filth, water, and low, and high temperatures.
Roller Types

HDPE Roller
The full name of HDPE roller is high-density polyethylene roller, it has better performance compared to traditional steel idler roller, having lager market. It has better corrosion resistance and abrasion resistance.

IMPACT Roller
The impact roller is used to reduce the impact of blanking on the conveyor belt at the receiving area of the belt conveyor. Impact rollers are very helpful to protect conveyor belt when the rock or other heavy material drop down.

GARLAND Roller
Garland roller comprises either 3-roller or 5-roller joined together at the ends of their respective shafts by special lugs, to form a continuous ’chain’ of roller. On either end of this ‘chain’, the shafts are connected to an attachment bracket which enables the roller set to be attached to the conveyor stringer structures.